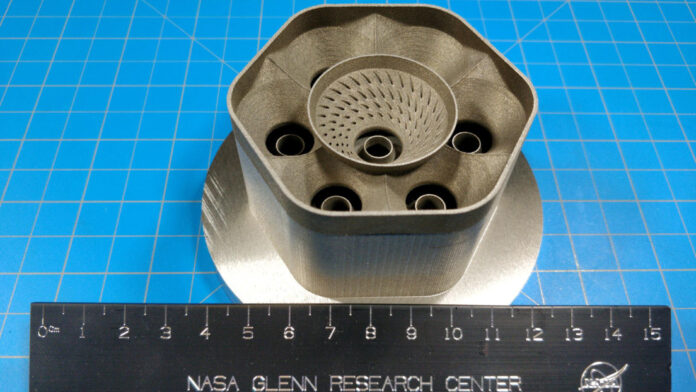
La NASA anunció la semana pasada la creación de un nuevo material destinado a mejorar “drásticamente la resistencia y la durabilidad” de los componentes de sus naves espaciales. Denominado como NASA Alloy GRX-810 y descrito por la agencia como “una aleación reforzada con dispersión de óxido”, tiene la capacidad de soportar temperaturas que superen 2.000 ºF, equivalentes a aproximadamente 1.093 ºC .
Además, la nueva aleación presenta propiedades como “el doble de fuerza para resistir la fractura, tres veces y media la flexibilidad para estirarse/doblarse antes de fracturarse y más de 1.000 veces la durabilidad bajo tensión a altas temperaturas“.
Gracias a estas características, el nuevo material es apto para emplearse en la fabricación de las piezas que componen los motores de aviones espaciales y cohetes. De acuerdo a la NASA, en el caso de los motores a reacción, la nueva tecnología también ayudaría a reducir el consumo de combustible y “generar menores costos de operación y mantenimiento”.
“Este avance es revolucionario para el desarrollo de materiales. Los nuevos tipos de materiales más fuertes y livianos juegan un papel clave en el objetivo de la NASA de cambiar el futuro de los vuelos“, aseguró Dale Hopkins, subdirector del Proyecto de Herramientas y Tecnologías de Transformación de la NASA. “Anteriormente, un aumento en la resistencia a la tracción generalmente reducía la capacidad de un material para estirarse y doblarse antes de romperse, razón por la cual nuestra nueva aleación es notable”, precisó.
Para desarrollar NASA Alloy GRX-810, el equipo de la agencia espacial utilizó modelos computacionales y descubrió la composición óptima de la aleación después de 30 simulaciones. Tras usar el sistema de modelado termodinámico, los investigadores recurrieron a la impresión 3D para “dispersar uniformemente los óxidos a nanoescala en toda la aleación” y proporcionarle propiedades mejoradas.
Fuente: actualidad.rt.com